Baltimore's Meyerhoff Hall Gets the Works
This article originally appeared in Auditoria Magazine, January 2002.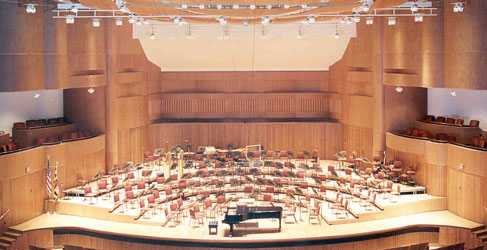
The musicians of the Baltimore Symphony Orchestra (BSO) were having trouble hearing each other during performances at Joseph Meyerhoff Symphony Hall, the 2,443 seat facilty that has been the orchestra's home since 1982. So orchestra and facility managers began working on a plan to improve the acoustics on and around the stage. But as discussions commenced with architects, consultants and technicians, the wish list began to grow and the project expanded dramatically.
By the time the BSO opened its 2001 season this September, five years after the original work began, Meyeroff Hall had received a complete $11 million renovation. Along with the comprehensive sound and design improvements in and around the stage, the musicians took their places in a hall featuring enhanced acoustics throughout, extensive rewiring, a fully modernized Electronic Theater Controls lighting system and a clear and powerful Meyer Sound speaker and sound control system.
The team brought together for the project included Baltimore architectural firm RTKL, acoustics experts Kirkegaard and Associates, theater design consultants Auerbach + Associates, installation specialists SPL Integrated Solutions, and rigging systems technicians JR Clancy.
One of the project's greatest hurdles was the orchestra's mandate against disruption of it's performance schedule. That meant that all work had to be performed during the brief window provided by the orchestra's summer hiatus each year. As Paul Garrity of Auerbach put it, "They had to take everything apart and put it back together again each summer."
While the Meyerhoff renovation ultimately encompassed new sound and lighting technology from floor to roof, the facility is first and foremost a symphonic hall, so the project was driven by the acoustic enhancements.
"The Meyerhoff people came to our company with a project that was relatively small in scope," explained Kirkegaard senior consultant Carl Giegold. "They were mostly thinking about reducing loudness on stage. As we got into examining the project with them, we began talking about other aspects of the building, and our role was extended to working out into the room itself, dealing with issues like harshness, presence and clarity, and echo control."
Over the five summers of the project, the renovation team reshaped the side walls of the auditorium, and constructed orchestra and chorus risers to improve ensemble conditions, enhancing clarity by getting more direct sound out to the audience as well as across the stage amongst the musicians. A piano lift and stage extension were constructed. The stage walls and a portion of the ceiling were reconstructed to eliminate thin plaster and other low frequency absorbers that had been weakening the acoustic response on stage, and the rear walls of the lower balcony were replaced with sound diffusers covered by perforated aluminum panels to help control echo.
The last phase, what Giegold called "the crown jewel," of the acoustic enhancements, was a new acoustic canopy, an array of fully adjustable fibreglass sound reflectors hung above the center of the stage. Said Giegold, "It did wonders for the clarity and presence out in the hall, as well as ensemble conditions and quality of tone on the stage."
As planning progressed, the decision was also made to provide Meyerhoff with an improved sound system. While orchestra itself performs unamplified, the BSO wanted to expand Meyeroff's range to allow a greater variety of Pops performances and concerts by popular performers of almost all kinds.
The lead team for the sound system redesign was Meyerhoff sound technician Randy Siegmeister, Garrity and Dan Mei of Auerbach, and independent SIM engineer Bob McCarthy.
While wiring and power systems were being reworked, a new 32-channel Soundcraft Series Five console was brought in. In addition, the Peavey MediaMatrix system used to provide centralized digital audio control, including all EQ delays and signal distribution, was upgraded to a 980nt Mainframe and an MM-8802 Break Out Box.
The Auerbach reps strongly recommended Meyer Sound equipment for Meyerhoff, and while Siegmeister required some convincing, extensive demonstrations and testing won him over. The configuration of Meyerhoff, and it's design as a primarily acoustic facility, became an issue for the team.
"As a concert hall," explained Garrity, "Meyerhoff is a liver room than a Broadway house would be. Also, it's a fairly deep room with high balconies and side boxes on the walls that wrap right around and even behind the edge of the stage. We had to be very careful that we would be hitting everybody but not exciting the room so much that we'd get a lot of reverberation."
The goal became a highly directional, tightly focused system that would deliver sound to the audience but not reach the walls or the ceiling. The Meyer Sound speaker array assembled to perform this tricky task included a top row of four MSL-4 Horn-Loaded Long-Throw Loudspeakers, a middle row of three CQ-1 Wide Coverage Main Loudspeakers, a bottom row of two UPA-1P Compact Wide Coverage Loudspeakers, plus an additional rear-facing UPA-1P used as an orchestra monitor. This cluster resides above the canopy when not in use and is lowered through a trap door in the canopy for those performances where amplification is in order. Due to size constraints, the PSW-6 High-Power Cardioid Subwoofer is dead hung above the canopy. Also in use are four UPM-2P Ultra-Compact Narrow Coverage Loudspeaker covering the side boxes. The speakers are controlled by Meyers RMS (Remote Monitoring System) 4.02 software.
One of the particular attractions of the Meyers speakers selected is that all but the UPM-2Ps are self powered; each speaker has its own built-in amplifier, a feature that helped the team overcome the space constraints they were working with.
"Meyer is one of the few manufacturers that's really moving forward with self-powered loudspeakers," explained Mei. "You don't have to have a separate rack of amplifiers. You just run your audio signal directly to the speaker and plug it in."
To make sure they were on the right track, the team took the unusual step of renting the exact array they were considering and installing it in the hall, rather than relying on computer simulation. Sound consultant Bob McCarthy was brought in to conduct a verification of the polarity and coverage of the system, and to optimize the relative level, relative delay, equalization and positioning of each component.
McCarthy's tool for this work was Meyer Sound's proprietary Source Independent Measurement (SIMŽ) programming. SIM uses program material as a reference to accurately compute the transfer function (amplitude and phase response) of each component of a hall or speaker system. Through McCarthy's testing, the Meyerhoff team could hear exactly how their proposed system would sound when optimized.
"That pre-installation testing was something special," McCarthy said. "Getting to shake out the entire system rather than relying on computer modeling was key. Normally I do a lot of post-computer work, where people are simulating away and I have to sort it out afterward, depending on how good their simulation was."
Once the final installation of the new speaker array was completed, McCarthy returned to ensure the optimization of the every aspect of the system. Said Siegmeister, "It turns out that the design is great, the coverage is extremely even, and everybody's extremely happy. It's exceeded my original expectations."
To complete the modernization and optimization of Meyerhoff, a new lighting system was installed, using equipment and programming from Electronic Theater Controls. The facility had been relying on an old Kliegel system that was no longer supported, and replacement parts were almost impossible to find. In addition, the system was inadequate both for Meyerhoff's newly enlarged stage and for the greater variety of theatrical and musical productions that the BSO had in mind for the revamped hall.
"We added a new concert lighting system," explained Auerbach lighting engineer Grace Gavin, "a downlight system that is fully integrated into the new canopy. Support battens, fabricated by JR Clancy, hang from the acoustic reflectors, and the light fixtures hang from those battens. We also installed a group of circuits that allows the BSO to add theatrical fixtures when they need them."
The new system greatly increases the flexibility of Meyerhoff's lighting, allowing it to be more zoned and more focusable, and creating new front of house positions to go along with the main beam position.
The Meyerhoff also received a new lighting control system using ETC NCE Network Configuration Manager software. Data from the control console is distributed digitally throughout the auditorium over a simple network, automatically manipulating devices like dimmers, scrollers and moving lights during performances.
"We've jumped up to the next generation of lighting control and data distribution network," explained Gavin. "We've got data distribution from the control room, we have it up in the attic area, we have it onstage and we also have a location in the pit where the lifts are, so if they ever need to get data down there they can do it."
Meyerhoff Hall's five-year renovation, a project that grew out of the musician's inability to hear each other performing, has been deemed a success by everyone involved.
Said Carl Giegold, "What was done in that room has a real sense of rightness to it. There is a general high level of enthusiasm for what was accomplished there."
« Go back